Sticking it to skin
The impact of wearable device material on successful adhesive choices
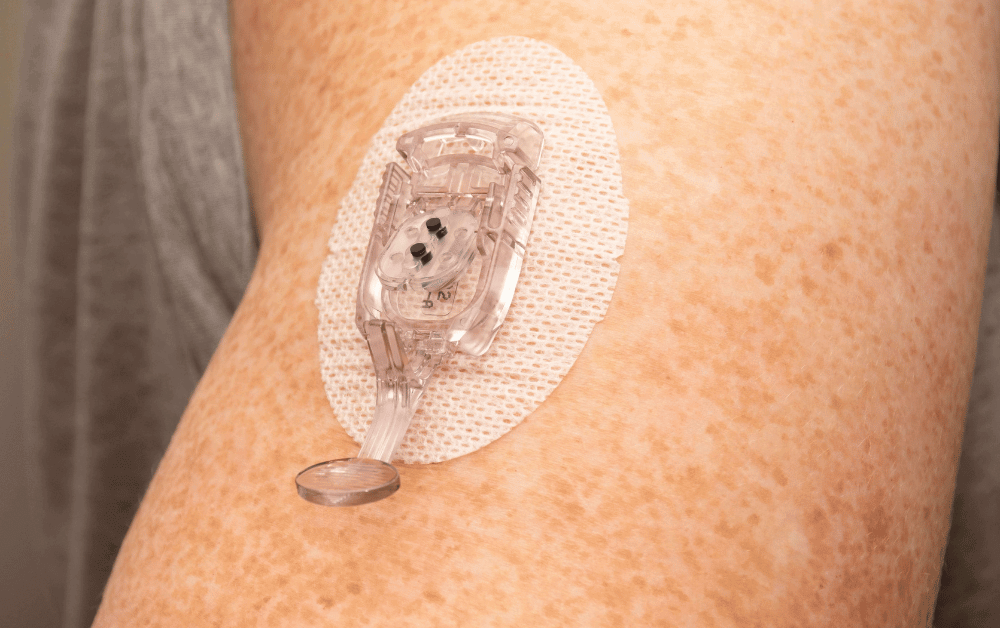
Advancements in medical wearable technology are improving device sizes, performance, wear time, and cost. These innovations mean improvements in electronics, such as smaller batteries and sensors, and computing software for data collection and monitoring are designed to be more compact and suit longer wear times. However, the wear time depends on adhesives and choosing the right one compatible with the device and the end user.
Developing a suitable adhesive begins in the development phase, where we consider the surface energy of the device materials and the skin. We align the differences between how our adhesives stick comfortably to the skin without restricting the end user’s movements and holding the device in place on the body so that it can perform according to its purpose.
In this article, we’ll share how surface energy determines which device materials and adhesives we select to bond with device materials and the skin.
Surface energy
Surface energy measures the attraction of a material to other materials through their molecular structure. Notably, it’s how liquid reacts on a surface. It is measured in a range between high surface energy to low surface energy. Surface energy regarding successful adhesive choices, means how easily or difficult adherence occurs between adhesives, wearable materials, and skin.
Here are some guidelines to differentiate between the two:
- If a material has a high surface energy, liquids will quickly spread out over the surface because that maximizes their intermolecular interactions. Examples of high surface energy materials that are commonly used to encase a wearable device are Polyester, Polycarbonate and Polyurethane.
- Liquids will tend to form droplets on the surface for low surface energy materials because that maximizes the intermolecular interactions within the fluid. Some typical examples of low surface energy materials are Silicone and Polypropylene.
Bonding easiest occurs between an adhesive and a substrate or surface when the surface energy is high, making it easier for it to “wet out”. Plainly stated, if the surface energy is low, the adhesive will bead and not cover the surface of the substrate, creating a weak bond. If the surface energy is high, the adhesive will spread and cover the entire surface, creating a solid bond.
Surface energy of different materials such as metals, ceramics, silica (silicates and glass), and graphite, have a high surface energy and quickly bond with adhesive applications. However, engineered polymers, hydrocarbon, fluorocarbon, and silicone polymers have low surface energy.
In the case of low surface energy materials, these materials can have other material characteristics that prove valuable, such as being good thermal or electrical conductors.
These varying characteristics are one of several reasons Avery Dennison must conduct testing on the specific material to develop suitable solutions and select the right adhesive to bond with the medical device.
Choosing the right materials
So far, we’ve discussed surface energy and the crucial role its understanding serves when selecting the suitable adhesive to bond with a device. Choosing the right materials for medical wearables and adhesives is about the complex balance between the device and the user. In other words, each layer of the wearable device must collect data, monitor users remotely, and not hinder user movement, all while fitting comfortably on the body. Let’s examine one of our case studies to emphasize the importance of meeting the demands of a complex balance between the device and the user.
Pilot applications: A case study
Avery Dennison conducted a 21-day wear time study, “Demonstrating 21-Day Wear Time for Medical Wearable Device Applications (February, 2023),” to design an extended wear adhesive for 21 days.
Healthy participants were selected to wear mock devices on the backs of their upper arms to record how long the device remained attached to the body before failing and to measure skin irritations on the body.
The study results showed that selecting the right materials for the adhesive must consider the adhesive chemistry, environment, device design, device location on the body, and skin factors. These considerations impact the overall wear performance.
Our commitment to quality
Avery Dennison collaborates with medical device companies and suppliers who are experts in materials science to develop medical wearable solutions. Together, we produce new product ideas and simple solutions.
We prioritize skin-friendly materials and timely solutions to meet the needs of wearable device companies and their users. We maintain transparency and credibility in our partnerships to comply with the FDA and other regulatory bodies.
Conclusion
Adhesive selection is contingent on the materials used in making a device and their wear time performance. A more thorough understanding of surface energy and the relationships between medical wearable devices and adhesive materials provides clarity in developing reliable products that comfortably perform for the end users.
At Avery Dennison, we are committed to quality through our collaborations and pilot applications to keep pace with the evolving medical wearable market.
About the Author
Miguel Solivan
Marketing and Product Manager, Medical
Miguel brings over 30 years of operations and marketing expertise to Avery Dennison's Performance Tapes Medical business. His focus lies in technical pressure-sensitive adhesive tape solutions, cross-company collaborations, and identifying innovative design opportunities and future trends within the Wearables, Wound Care, Surgical, and Ostomy markets.
Email Miguel at medical.solutions@averydennison.com